Design and finite element analysis of a 3D-printed packaging insert
DOI:
https://doi.org/10.37636/recit.v6n3e254Keywords:
Packaging insert, Finite element analysis, 3D printingAbstract
Packaging inserts play a crucial role in protecting products during transportation. However, their design and production processes often rely on conventional methods limiting equipment capabilities. Moreover, the empirical nature of their design can result in a lack of reliability in the final product. To address these challenges, this study aimed to validate the design of a packaging insert using the finite element method and subsequently create it using 3D printing. The chosen material is a thermoplastic polyurethane (TPU) filament commonly used in fused deposition filament printers for 3D printing. This process demonstrates the feasibility of using 3D printing to create cushioning inserts for packaging and employing finite element analysis to simulate the insert behavior. The main findings of this research highlight the potential benefits of numerical simulation, revealing the areas where the insert is primarily impacted by weight. Furthermore, the forces load and displacement simulation results confirm that the TPU elastic limit (3.9x106 MPa) is sufficient to handle the weight this insert intends to hold. These tools determine the viability of the proposed design for its intended application. Therefore, this study verifies that 3D printing is a reliable option for producing packaging inserts, offering significant advantages over traditional methods. These advantages include increased design flexibility and the ability to create custom inserts on demand.
Downloads
References
United Parcel Service of America, "UPS," [Online]. Available: https://www.ups.com/us/en/home.page. [Accessed: Apr. 5, 2023].
A. Emblem, Ed., Packaging Technology: Fundamentals, Materials, and Processes. Elsevier, 2012. DOI: https://doi.org/10.1533/9780857095701
R. Hernandez, S. Selke, and J. Culter, Plastics Packaging. Munich: Hanser, 2000.
G. Giles and D. Bain, Eds., Technology of Plastics Packaging for the Consumer Market. Oxford, UK: Wiley, 2001.
N. Theobald and B. Winder, "Packaging Closures and Sealing Systems," Sheffield Academic Press, Sheffield, 2006. [Online]. Available: http://www.sheffieldacademicpress.com/books/technology/packaging-closures-and-sealing-systems. [Accessed: Apr. 5, 2023].
J. P. Kruth, G. Levy, F. Klocke and T. H. C. Childs, Eds., Additive Manufacturing: Second Edition. Boca Raton, FL: CRC Press, Taylor & Francis Group, 2020.
A. Cattenone, S. Morganti, G. Alaimo, and F. Auricchio, "Finite element analysis of additive manufacturing based on fused deposition modeling: Distortions prediction and comparison with experimental data," Journal of Manufacturing Science and Engineering, vol. 141, no. 1, p. 011008, Jan. 2019. https://doi.org/10.1115/1.4041626 DOI: https://doi.org/10.1115/1.4041626
International Trade Center. (2010). Packaging design: A practitioner's manual. Geneva, Switzerland: International Trade Center UNCTAD/WTO.
I. Blanco, "The use of composite materials in 3D printing," Journal of Composites Science, vol. 4, no. 2, p. 42, 2020. https://doi.org/10.3390/jcs4020042 DOI: https://doi.org/10.3390/jcs4020042
H. A. Colorado, E. I. G. Velásquez, and S. N. Monteiro, "Sustainability of additive manufacturing: the circular economy of materials and environmental perspectives," Journal of Materials Research and Technology, vol. 9, no. 4, pp. 8221-8234, 2020. https://doi.org/10.1016/j.jmrt.2020.04.062 DOI: https://doi.org/10.1016/j.jmrt.2020.04.062
N. Elmrabet and P. Siegkas, "Dimensional considerations on the mechanical properties of 3D printed polymer parts," Polymer Testing, vol. 90, p. 106656, 2020. https://doi.org/10.1016/j.polymertesting.2020.106656 DOI: https://doi.org/10.1016/j.polymertesting.2020.106656
B. Wittbrodt and J. M. Pearce, "The effects of PLA color on material properties of 3-D printed components," Additive Manufacturing, vol. 8, pp. 110-116, 2015. https://doi.org/10.1016/j.addma.2015.09.006 DOI: https://doi.org/10.1016/j.addma.2015.09.006
M. Schmitt, R. M. Mehta, and I. Y. Kim, "Additive manufacturing infill optimization for automotive 3D-printed ABS components," Rapid Prototyping Journal, vol. 26, no. 1, pp. 89-99, Jan. 2020. https://doi.org/10.1108/RPJ-01-2019-0007 DOI: https://doi.org/10.1108/RPJ-01-2019-0007
R. S. Ambekar, B. Kushwaha, P. Sharma, F. Bosia, M. Fraldi, N. M. Pugno, and C. S. Tiwary, "Topologically engineered 3D printed architectures with superior mechanical strength," Materials Today, vol. 48, pp. 72-94, 2021. https://doi.org/10.1016/j.mattod.2021.03.014 DOI: https://doi.org/10.1016/j.mattod.2021.03.014
ASTM International, "Standard test method for tensile properties of plastics," ASTM D638-14, West Conshohocken, PA: ASTM International, 2018.
International Organization for Standardization, "Plastics Determination of tensile properties Part 1: General principles," ISO 527-1:2019, 2019.
A. El Moumen, M. Tarfaoui, and K. Lafdi, "Modelling of the temperature and residual stress fields during 3D printing of polymer composites," The International Journal of Advanced Manufacturing Technology, vol. 104, pp. 1661-1676, 2019. https://doi.org/10.1007/s00170-019-03965-y DOI: https://doi.org/10.1007/s00170-019-03965-y
T. Yao, Z. Deng, K. Zhang, and S. Li, "A method to predict the ultimate tensile strength of 3D printing polylactic acid (PLA) materials with different printing orientations," Composites Part B: Engineering, vol. 163, pp. 393-402, 2019. https://doi.org/10.1016/j.compositesb.2019.01.025 DOI: https://doi.org/10.1016/j.compositesb.2019.01.025
P. Wang, B. Zou, H. Xiao, S. Ding, and C. Huang, "Effects of printing parameters of fused deposition modeling on mechanical properties, surface quality, and microstructure of PEEK," Journal of Materials Processing Technology, vol. 271, pp. 62-74, 2019. https://doi.org/10.1016/j.jmatprotec.2019.03.016 DOI: https://doi.org/10.1016/j.jmatprotec.2019.03.016
J. Zhang, Y.-G. Jung, and C. Additive Manufacturing: Materials, Processes, Quantifications, and Applications. Butterworth-Heinemann. 2018. DOI: https://doi.org/10.1016/B978-0-12-812155-9.00002-5
ISO/ASTM52900-15, "Standard Guide for Additive Manufacturing - General Principles - Terminology," International Organization for Standardization and ASTM International, West Conshohocken, PA, 2015.
Z. Andleeb, H. Khawaja, K. Andersen, and M. Moatamedi, "Finite Element Analysis to determine the impact of Infill density on Mechanical Properties of 3D Printed Materials," in Proceedings of the 2022 International Conference on Additive Manufacturing and 3D Printing, TBD. https://doi.org/10.21152/1750-9548.16.3.317 DOI: https://doi.org/10.21152/1750-9548.16.3.317
M. Scapin and L. Peroni, "Numerical simulations of components produced by fused deposition 3D printing," Materials, vol. 14, no. 16, pp. 4625, 2021. https://doi.org/10.3390/ma14164625 DOI: https://doi.org/10.3390/ma14164625
M. Alharbi, I. Kong, and V. I. Patel, "Simulation of uniaxial stress–strain response of 3D-printed polylactic acid by nonlinear finite element analysis," Applied Adhesion Science, vol. 8, no. 1, pp. 1-10, 2020. https://doi.org/10.1186/s40563-020-00128-1 DOI: https://doi.org/10.1186/s40563-020-00128-1
J. Zhang, X. Z. Wang, W. W. Yu, and Y. H. Deng, "Numerical investigation of the influence of process conditions on the temperature variation in fused deposition modeling," Materials & Design, vol. 130, pp. 59-68, 2017. https://doi.org/10.1016/j.matdes.2017.05.040 DOI: https://doi.org/10.1016/j.matdes.2017.05.040
H. Xia, J. Lu, and G. Tryggvason, "A numerical study of the effect of viscoelastic stresses in fused filament fabrication," Computer Methods in Applied Mechanics and Engineering, vol. 346, pp. 242-259, 2019. https://doi.org/10.1016/j.cma.2018.11.031 DOI: https://doi.org/10.1016/j.cma.2018.11.031
A. Chadha, M. I. Ul Haq, A. Raina, R. R. Singh, N. B. Penumarti, and M. S. Bishnoi, "Effect of fused deposition modelling process parameters on mechanical properties of 3D printed parts," World Journal of Engineering, vol. 16, no. 4, pp. 550-559, 2019. https://doi.org/10.1108/WJE-09-2018-0329 DOI: https://doi.org/10.1108/WJE-09-2018-0329
S. Garzon-Hernandez, D. Garcia-Gonzalez, A. Jérusalem, and A. Arias, "Design of FDM 3D printed polymers: An experimental-modelling methodology for the prediction of mechanical properties," Materials & Design, vol. 188, p. 108414, 2020. https://doi.org/10.1016/j.matdes.2019.108414 DOI: https://doi.org/10.1016/j.matdes.2019.108414
A. Armillotta, M. Bellotti, and M. Cavallaro, "Warpage of FDM parts: Experimental tests and analytic model," Robotics and Computer-Integrated Manufacturing, vol. 50, pp. 140-152, 2018. https://doi.org/10.1016/j.rcim.2017.09.007 DOI: https://doi.org/10.1016/j.rcim.2017.09.007
S. Wickramasinghe, T. Do, and P. Tran, "FDM-based 3D printing of polymer and associated composite: A review on mechanical properties, defects, and treatments," Polymers, vol. 12, no. 7, p. 1529, 2020. https://doi.org/10.3390/polym12071529 DOI: https://doi.org/10.3390/polym12071529
N. González-Bautista, V. H. Mercado-Lemus, M. Hernández-Hernández, H. Arcos-Gutierrez, and I. E. Garduño-Olvera, "Methodology to implement CAE validation in repair & redesign parts process of plastic injection molds," Revista de Ciencias Tecnológicas, vol. 5, no. 1, pp. 176-193, 2022. https://doi.org/10.37636/recit.v51176193 DOI: https://doi.org/10.37636/recit.v51176193
T. S. Tamir, G. Xiong, Q. Fang, Y. Yang, Z. Shen, M. Zhou, and J. Jiang, "Machine-learning-based monitoring and optimization of processing parameters in 3D printing," Int. J. Comput. Integr. Manuf., vol. 35, no. 3, pp. 1-17, 2022. https://doi.org/10.1080/0951192X.2022.2145019 DOI: https://doi.org/10.1080/0951192X.2022.2145019
P. D. Nguyen, T. Q. Nguyen, Q. B. Tao, F. Vogel, and H. Nguyen-Xuan, "A data-driven machine learning approach for the 3D printing process optimisation," Virtual and Physical Prototyping, vol. 17, no. 4, pp. 768-786, 2022. https://doi.org/10.1080/17452759.2022.2068446 DOI: https://doi.org/10.1080/17452759.2022.2068446
S. Nasiri and M. R. Khosravani, "Machine learning in predicting mechanical behavior of additively manufactured parts," Journal of materials research and technology, vol. 14, pp. 1137-1153, 2021. https://doi.org/10.1016/j.jmrt.2021.07.004 DOI: https://doi.org/10.1016/j.jmrt.2021.07.004
G. D. Goh, S. L. Sing, and W. Y. Yeong, "A review on machine learning in 3D printing: applications, potential, and challenges," Artificial Intelligence Review, vol. 54, no. 1, pp. 63-94, 2021. https://doi.org/10.1007/s10462-020-09876-9 DOI: https://doi.org/10.1007/s10462-020-09876-9
Dassault Systèmes SolidWorks Corp., SolidWorks [Computer software], Available: https://www.solidworks.com/
V. V. Mazur, "Theoretical study of the force heterogeneity of airless tires made of elastic polyurethanes," vol. 1, pp. 891, 2021. https://doi.org/10.1007/978-3-030-85233-7_2 DOI: https://doi.org/10.1007/978-3-030-85233-7_2
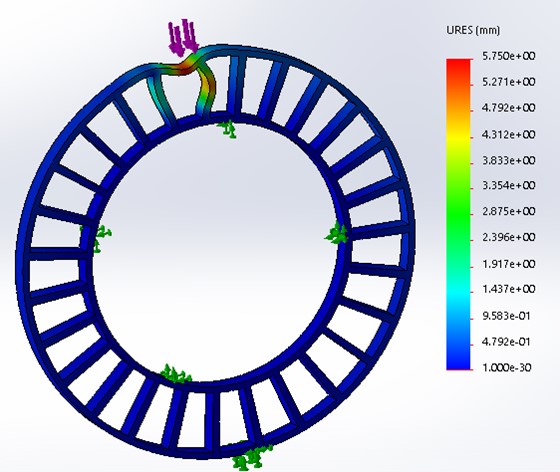
Published
How to Cite
Issue
Section
Categories
License
Copyright (c) 2023 Ismael Alejandro Muñoz Salazar, Isaías Emmanuel Garduño Olvera, Mayra del Angel Monroy

This work is licensed under a Creative Commons Attribution 4.0 International License.
The authors who publish in this journal accept the following conditions:
The authors retain the copyright and assign to the journal the right of the first publication, with the work registered with the Creative Commons Attribution license 4.0, which allows third parties to use what is published as long as they mention the authorship of the work and the first publication in this magazine.
Authors may make other independent and additional contractual agreements for the non-exclusive distribution of the version of the article published in this journal (eg, include it in an institutional repository or publish it in a book) as long as they clearly indicate that the work it was first published in this magazine.
Authors are allowed and encouraged to share their work online (for example: in institutional repositories or personal web pages) before and during the manuscript submission process, as it can lead to productive exchanges, greater and more quick citation of published work (see The Effect of Open Access).